Setting up a Dovetail jig
Personally I thought all those promo videos for dovetail jigs were a bit
suspicious. They just can't come out of the box and cut beautiful dovetails at
once like the guy in the video seems to. They are going to need a bit of
setting up and that they'll need to be carefully adjusted for the stock you are
cutting and that includes selecting the right cutting tool. There can't be one
jig set up and one tool that cuts all jobs.
I am a retired physicist and this page details my journey through setting up a
cheap jig and the calculations you need to do to even cut a joint that goes
together given the cutting tools you have. Yes. There will be sums.
So I bought this cheap Lumberjack DTJ300 jig to cut dovetail joints on my also
cheap router and it's got problems. Well, let's say I was a trifle
disappointed. Primary school design, third world engineering and obvious fuzzy
bits in the manual. This is strange as I see exactly the same item with
different badges. (eg: as a Clarke CDTJ12, or a blue one I saw on Ebay with no
'manufacturer' plate.) I decided that the best way to preserve what little
remains of my sanity was to understand it then write the setup and user guide
it really needed. I rather doubt that the manufacturers will thank me but the
other owners might as it can do the job given quite a bit of engineering
care.
BUT PLEASE:
If you want to use this as a guide please read the whole thing first and decide
if you are up to this amount of hacking and is it worth the extra bits you may
need for what it can do at the end.
Tools wise you need a No. 2 Phillips screwdriver, a 12mm spanner, a good metal
square and a decent measuring calliper. I suspect that a good metalworking vice
and a set of files ought to be on the list too. For the calliper a single place
of decimals on the mm is probably OK but if your buying get two and be sure you
get the type with the depth gauge tail. You will want this whenever you reset
things for a different size of wood. Also get the nice one in metal.
They say you should screw it to a bench but if you have spare benches around to
use you wouldn't be buying tools at this end of the market. I found a nice
piece of off cut worktop my brother threw out that would G-clamp to the 'ol B&D
Workmate and used that.
Start by taking the loose bits off again. Undo the four big wheels but slide
your fingers under things to catch the springs before they escape and you have
to chase them under the bench. Put these to one side carefully. Now you can get
at the screw holes to screw it down. Get your alignment right here as you don't
want to twist anything.
Right. That front edge bend is your reference line. We will measure right
angles from that and from that only. Right angles are very important today so
be careful.
Now set things up. They start by telling you to mark a pencil line in the
middle of a finger. This is sets the starting point of the dovetails. This
makes the edge that is cut against the guides the 'nice' edge. Both edges can
be 'nice' if your stock is almost an exact number of old imperial half inches
wide but I will discuss what I mean by 'nice' later. Pull the template towards
you when setting this position as that takes up a lot of the slop. If you then
always pull on the template as you close the top clamp you will return to this
position.
My template and my base are only nearly the same size but the left hand edges
aligned rather well. This meant I could measure the position of the line and
then transfer the measurement to the bed and set the stop. Then I ran a finger
down the edge of the stop and it was lumpy. Lumpy?! Yes, I know this is 'only'
woodworking gear but it came out, it went in the vice and it was draw-filed
flat to match the square. This was my first 'OMG what have I bought?' moment.
There were many more to come.
My stop had enough slop in it to set it to a true right angle here. I view the
right angle here as critical. If your stock doesn't align up on the stop it
isn't square and if it isn't square your results will be horrible. See my next
stage for what you may face here.
Now to the front stop. This wants to be a further 0.5" to the right and another
dead on the money right angle to our reference edge. Mine wasn't going to play
right angles and I looked at it and wondered if it would bend straight but I
decided against trying so it got over a mm filed off the top end edge in
addition to becoming flat.
Also check if the top of front stop sticks up above the top surface. If it does
cut it back until it doesn't. A couple of extra millimetres here don't add any
stability but it does restrict how close to the deck you can cut.
Now be careful because this 0.5" offset is totally mission critical for the
alignment so go the extra mile to get it right and check that it is so. I used
a nice steel rule that was impeccably straight to carry the position over to
the square on the edge. These positions are then fixed for this template and
I'm pretty sure there are no other templates available.
Great. Now go to the other end and do it too. Exactly the same but mirror
image. All will be explained later.
Right. That's part one done. You now have the base all set-up to match your
template. We can put the other bits back on again.
Check you have the handles right. The front grip wants to be closed when the
handle points down and the top one wants to be closed when it points away from
you. If they are not that way round they will get in the way when you are
cutting so screw them in from the other side. My way of using the clamps is to
start with the handles open and a piece of wood at both ends and wind the knobs
down until they grip the work piece. Then back off each knob one full turn. Now
the handles just work as an open-close and the last bit on the cam really locks
things down. Just remember what I said about pulling the template towards you
as you close the top clamp.
So now it begins to look like mine and you want to cut something? OK did it
come with a 'free' tool like the one on the right? 1/2" x 1/2" x 14° It
did? Drat. I hoped they would have fixed that by now. That is a half inch
cutter that at cuts a half inch deep slot with a half inch bearing and you have
a half inch template so you're stuffed. Time for some explanations I guess. Yes
I do mean sums.
Right here is an end on picture of a dovetail joint and let's assume you cut it
on this rig.
That means it is a half inch sequence so a peg then a slot every half inch and
the pattern repeating every whole inch. What do you notice about the pegs and
slots? They have a big end and a little end. So the big end must be more than
half an inch and the little end must be less.
The tool that came with mine was half an inch at the widest end and had a half
inch bearing so it was a pretty exact fit to the slots in the template. It cut
a very nice dovetail slot but it was half an inch wide at the bottom and the
peg it leaves behind is too big to fit in the hole it cuts.
It would cut a mean dovetail on a template with half inch wide slots and
quarter inch wide fingers. Trend make a nice one but it costs more than I paid
for this whole jig. Now don't throw the tool away. There is a frig that might
make use of it but I'll come back to that later.
What I needed was a larger tool so it cut a larger slot in one pass.
'Larger' is not the only problem. The big end and the little end must add up
exactly to one inch. Obvious isn't it?
This means that any tool has a 'correct' cutting depth where the diameter at
the top of the cut is just right to add up with the diameter at the bottom to
match your jig size (well twice the jig size obviously). A cut with the
supplied tool into a piece of 12mm ply is shown below right. Obviously, as long
as the tool is constrained to the slot in the template it cannot cut an equal
set of dovetails.
On the right is a 5/8" x 9/16" x 14° tool I bought on Amazon. Annoyingly it
was only available on next day paired with a 1/2" x 1/2" x 10° tool but
when I discovered that the 5/8" tool was supplied with a 15mm bearing I swapped
on the 1/2" one from the 1/2" tool and so got some value from
it.
So... This is a 5/8" tool with 9/16" maximum cut depth and a 14° angle. The
angle is very important.
Time to revise your school maffs. Tangent is opposite over adjacent.
Remember?
The diagram is of the edge of the tool where d is the depth of cut and
n is how much narrower the cutter is at the top of the hole on this
side. Hence the actual cut diameter has decreased by 2 times n.
Of course the tool might be longer than the depth of cut we want but that bit
of the cutter just sticks out above the wood.
Call up Windows calculator. Scientific mode. Check it is in DEG mode (not RAD
or GRAD - first thing below the result display). Type in:
1 4 Pull down the Trigonometry menu and select tan x 0 . 5 =
It should say 0.12466400142159034581201996890243 which is within a tiny
fraction of 0.125 ie. 1/8 so by cutting 1/2" deep we have decreased the radius by 1/8"
and hence the diameter by 1/4". Therefore our hole is 5/8" wide at the bottom
and 3/8" at the top and also the top plus the bottom is one inch so we have a
nice tight dovetail on one tool.
You can reverse the calculation and work out the depth of cut needed for a
given size as d = n/tan a remembering that n is half the decrease
in diameter you want.
The next problem is that for a true dovetail the dovetail router might do one
half but the other half would have to be done with a parallel sided router
because if you pull out before the end the router must leave a curve. This
means you could not machine them with a single tool and certainly not in a
single pass.
This is resolved by allowing for a circular end to the hole but cutting a
matching curve to go into it and then burying it all inside the
joint.
Right. Let's set things up and cut some wood.
Our workpiece must be thicker than 1/2" deep (12.7mm) as that is the cut depth for the
tool. I have some cheap 18x70mm (actually 17.7x69.8 over several measurements
so not bad) and I've bandsawed off several 200mm lengths. It clamps into the
jig so the bit in the front overlaps the bit on the top. Remember it goes in
'inside out'. Think of it as a box and we always cut it with the inside faces
of the box on the outside. The 'nice' edges, that would be the top of the box,
go against the stops.
To stop my brain from exploding I'm going to use a simple
convention here. Most things will just have a single capital letter for their
value however for round things we are jittering back and forth between
measuring distances by their radius and referring to the size in the
specification that is a diameter. I will use a lower case letter for the radius
and a capital for the diameter. eg: my bearing is half an inch in diameter
B but a quarter of an inch in radius b.
There are three crucial settings
First we need to set the template position. Here we are setting the depth of
cut on the tips of the curved ends of the pegs which will finally be buried
within the joint. I will call it M. It can be small, zero or even
negative (which only gives us a flat bit), but that cannot be seen once the
joint is assembled. This tool is cutting 3/8" (9.524mm) diameter at the
surface.
Consider my diagram:
The black line represents the template, the brown is the edge of the wood, the
red is the bearing as we come round the tip of the template finger being the
point of minimum cut and the blue is the cutting radius at the set depth of
cutter: ie at the surface of the work. We want to work out how far from the
edge of the wood should the end of the finger be to get the desired amount of
cut here.
Step it with me. Starting from the edge of the wood go in by M the
margin we want to cut the end of the curve. This takes us to the blue circle,
the cutter. This is a plus distance. Then go back by the cutter radius c
(small end at the surface of the wood) to get to the centre of the router
spindle. Then go forward by the radius of the bearing b and we should
now be on the tip if the finger. D = M - c + b
Since we always think of these things in diameters make that
D = M + (B-C)/2
My Bearing B is 1/2", my cutter C is 3/8" at the top so
(B-C)/2 is 1/16" say 1.6mm so I'll go for 2mm to give me 0.4mm of
margin so the cutter does actually cut something all round the curve.
Put pieces of material in all four positions, top, front, left, right and don't
forget to pull the template forwards when clamping the top, then slacken the
little knobs at the back and set the position of the template relative to the
edge of the wood in the front clamp to D. Yes I know the knobs foul one
another. Some M10 washers under the big ones helped on one side for me but I
had to use a grindstone to reduce both small wheels down a bit to make it
actually work. (sigh)
Now we need to set the horizontal distance we want to cut. So how far is
that?
What we want to do is bury the peg we cut in the front bit of wood into the
hole we cut in the back bit. The peg, at its longest, is the thickness of the
wood W less the margin M we used in the previous calculation so
W-M (the blue line in picture). Hence we want to cut right through the
front piece of wood and then W-M into the end of the other bit (the red
line) so we are cutting 2*W-M total depth into the wood.
This is, of course, measuring to the largest radius of the cutter k so
the spindle needs to go to 2*W-M-k deep into the wood measuring from the
front edge of the wood. Finally add the distance from the spindle of your
router to the edge that will contact the stop S giving 2*W-M-k+S
as the distance from the front of the wood to the stop.
My router is 55mm from the spindle to the edge, my wood is 17.7mm, my margin
was 0.4mm and k is half of 5/8" so 7.94mm giving 2*W-M-k+S as
82.06 measuring from the edge of the wood and hence 80.06 if you measure from
the end of the template finger using the value of D we just
set.
If you use the formula in the manual it has already told you to use 3mm for
D which implies 1.4mm of margin with my cutter and that gives 82.46mm
whereas my formula would give 81.06.
And now set the cutter depth. My template is 5.7mm thick and as I want a
12.7mm, half an inch, depth of cut into the wood for all the sums to work out I
need it to project 18.4mm below the router bottom plate.
Do you see the snag in the picture?
Oh No!
The bearing isn't deep enough to engage with the template.
Right. This is OK. There are two ways to manage this and I will try to
demonstrate them both but I need another part for the second one.
I found a piece of horrible laminate board in the scrap bin. True bonfire
material but a very consistent 5.2mm thick so I cut a panel 300mm wide and slid
it over the workpiece coming forward to just over one workpiece thickness from
the edge of the piece of wood on top. If something goes wrong and it slips into
the blade I have more. Now I increase the cutter depth by 5.2mm to
23.6mm.
Put it all back together, put my carefully squared timber in (If you are trying
to cut dovetails and you haven't bothered to true up your stock... Well you
mother is a hamster and your father smells of elderberries.) I run my fingers
between the template's fingers to prove how aligned it all is and it isn't. It
was! It was just moments ago! New snag. When I tighten the top clamp at the
back the front lifts.
So what's the matter? Well the problem is that the base isn't flat. This was a
real "OMG do I just give up now?" moment.
OK. Slow down. It was OK when gravity lay my short piece of board on the front
edge of the bed but failed when the big butch clamp aligned it to the back of
the bed. I can't fix it, this would have been relatively trivial to the press
break operator forming it if somebody had pointed out that it would be a
problem, but can I fudge it now?
Try a good ol' woodworking cramp. Well that pulls it back into line but where
can I put a cramp where it won't foul the router path? No. That's not the way.
Try to pad the back of the bed.
Measure it. 1.3mm would do nicely. Measure every bit of metal plate I have and
only the steel ruler is close to right. Reassemble it with that just for a
test. This time nothing changes when I do up the clamp so nothing is able to
flex as I cut so I order up some 1.5mm Ali to do a more permanent job with a
couple of pop rivets.
Time to cut some wood.
The settings are checked as D=2mm, DEC=80.06mm from the fingers and 23.6mm tool
depth.
Well I'd like to say it wasn't bad for a first attempt but of course it wasn't
the first. The first was after carefully following the instructions in the
manual which left me looking at what I had just made in abject horror writing
numbers and drawing diagrams on a post-it and slowly realising that the jig and
the cutter that I had could never achieve anything that would actually even go
together and, hence, sending me off into engineer mode.
Well it's a nice snug joint. It slides together when you press firmly and won't
fall apart. The two parts come together flush and feel flush as you run your
fingers over them so the depth of cut is cool.
There is a 0.5mm gap below the tenons. This tells me I need to cut about 0.2mm
deeper, or perhaps refine my method of measuring the cutter position. This will
also make it tighter so probably promoting it to 'knock it together'
status.
However there is a 1.5mm offset between the parts. I thought this was all
controlled by the 0.5" separation between the stops. I am absolutely sure I was
tight up against my stops. I clearly haven't finished yet.
It's now better than I could cut by hand.
I checked my maths and I trust it so I go and reset the 0.5" offsets and then
come back and set things up again. The router proves itself not very good at
repeating a setting.
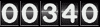